
Environmental protection at Pirdop
Aurubis Bulgaria is the largest copper producer in southeastern Europe and the second largest company in Bulgaria. Since the Pirdop site was officially opened in 1958, mainly copper anodes, copper cathodes, and sulfuric acid have been produced from primary raw materials.
Aurubis Bulgaria is the largest copper producer in southeastern Europe and the second largest company in Bulgaria. Since the Pirdop site was officially opened in 1958, mainly copper anodes, copper cathodes, and sulfuric acid have been produced from primary raw materials here.
In the last two decades, the plant has been converted into a highly modern, environmentally friendly operation. Since the acquisition by Aurubis in 2008, around € 165 million has been invested in modernizing the processes and improving the environmental performance of the site.
Because improving environmental protection remains a very important objective, about 20 % (~€ 75 million) of all investments at the site in the last five years have been allocated to environmental protection projects.
In the course of the extensive modernization, three significant, state-of-the-art environmental protection facilities have been built in the last several years. In November 2014, a new rainwater treatment plant was commissioned. The facility treats rain and drainage water from the 4 km² plant premises in order to continue reducing emissions to water.
A new additional treatment system for secondary hood off-gases has been in operation since March 2016. The new system utilizes a modern procedure known as Sulfacid technology, which is unique in Bulgaria and in the entire copper smelting industry.
In addition, a converter slag cooling optimization project (using pot cooling instead of pit cooling) went into regular operation in early 2020. This new facility further reduces the sulfur dioxide emissions and fugitive emissions from the smelting processes. The project will be expanded during the next several years to optimize cooling of the slags from the flash smelting furnace as well. The permit for the expansion was obtained in July 2024 and the construction started in September of the same year. More than 11,000 m² of green areas will also be rehabilitated as part of the project.
Aurubis assumes responsibility for environmental conservation. The plant is located near nature conservation areas. The closest are the Tsentralen Balkan buffer, about 1 km away, and Sregdna Gora about 2 km away. Protecting nature and biodiversity is one of our environmental targets, and Aurubis Bulgaria has defined measures to improve the habitat conditions of plants and animals. For example, we have taken the initiative to rehabilitate areas by planting grasses, bushes and trees. Defunct landfill areas on the premises are renatured in the course of their closing. Other environmental projects to reduce emissions likewise have a positive impact on the environment. For example, the reduction in metal emissions to water, which have been reduced by over 98 % since 2000, improves habitat conditions in rivers.
In 2006, Aurubis Bulgaria introduced an environmental management system in accordance with the ISO 14001 standard. The last recertification was successfully concluded in March 2024. The external audits carried out as part of the certification of the management system include a review of the environmental data, of the fulfillment of legal provisions, and of the effectiveness of the operating processes. During the second half of 2022, the energy management system pursuant to ISO 50001, the occupational health and safety management system pursuant to ISO 45001, and the quality management system were implemented at the Pirdop site.
Since 2011, an information center has been operating in Pirdop, which is used by the general public for information purposes. The environmental monitoring data can also be viewed by the public on monitors in the municipalities of Pirdop and Zlatitsa.
The results of the environmental monitoring are transmitted to the authorities. The reports prepared annually can be viewed on the homepage of the Bulgarian Executive Environment Agency.
The Pirdop site has been part of the EU emission trading scheme since 2008 and has continuously improved its energy efficiency over the years. Aurubis Bulgaria intends to make further investments in environmental measures and energy efficiency improvements in the future as well.
Environmental Protection Pirdop - facts & figures
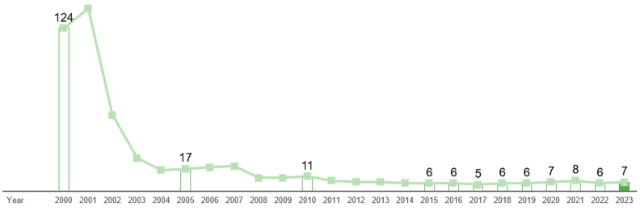
SO2 emissions [kg/t] per ton of copper output
SO2 emissions per ton of copper output have been reduced by 95 % since 2000.
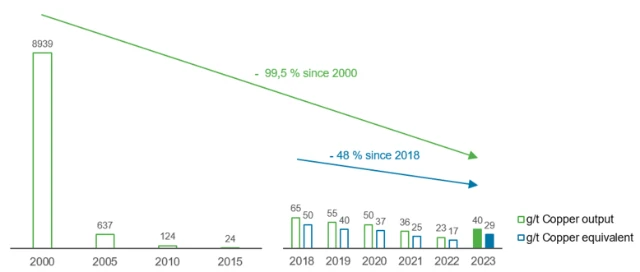
Dust emissions [g/t] per ton of copper output
Dust emissions per ton of copper output have been reduced by 99.5 % since 2000.
Key factors in the reduction of dust and SO2 emissions include:
- a number of modernizations in both lines of the Sulfuric Acid Plant (2001–2014)
- the replacement of the heavy oil dryer with a steam dryer (2001–2002)
- the first (conventional) off-gas cleaning system for secondary hood off-gases (2007)
- the new additional (Sulfacid) off-gas cleaning system for secondary hood off-gases (2016)
- the new facility for cooling converter slag in pots (2020)
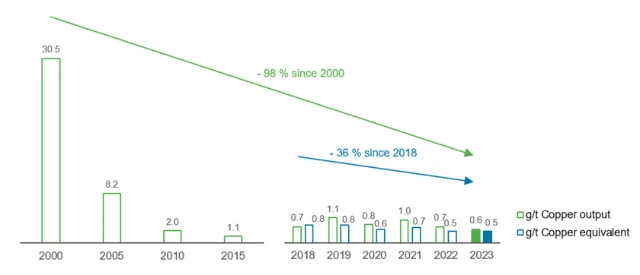
Metal emissions in g/t of copper output and in g/t of copper equivalent
The specific metal emissions to water per ton of copper output have been reduced by 97 % since 2000.
Key factors in the reduction of metal emissions to water include:
- the commissioning of the second and third stages of the treatment plant for industrial wastewater (2005-2006)
- the modernization of the wastewater system for acidic wastewater (2006-2008)
- the modernization of the wastewater systems for domestic sewage (2010-2011) and rainwater (2012-2013)
- the commissioning of the rainwater treatment plant (2014)
- the commissioning of a sand bed filter unit in the industrial wastewater treatment plant (2020)
Due to a new process of the planned upgrade of the wastewater treatment plant at Pirdop site, the amount of sludges for landfilling (generated during production processes in Pirdop) and the chemical consumption will be reduced. This will extend useful lifetime of the landfill for the sludges. Furthermore, the upgrade will increase the WWTP treatment volume capacity for a most efficient wastewater treatment. The construction started in September 2024 and the commissioning is planned in Q1 2026.
Environmental Protection Measures & Projects
Degree of implementation/date/next steps:
-
Constructing a new facility for cooling converter slag in pots.
- Building permit received in Feb 2018
- Commissioned in Q1 2020
Status:
- Done
-
Extension of the project to further optimize the flash smelter furnace slag cooling process until Q3 2025
Degree of implementation/date/next steps
-
Installing a new sand bed filter unit in the industrial wastewater treatment plant
-
Building permit by October 2018
-
Commissioned in 2020
Status:
- Done
Degree of implementation/date/next steps
- Investigation of optimization possibilities finished
- Implementation done during the large-scale facility overhaul (Q2 2019)
Status:
- Done
- Existing bag filters modified and additional filter boxes installed
Next steps:
- Building permit received
- Landfill area renatured
Status:
- Finished in Q3 2021
Degree of implementation:
- Signed agreement with CEZ ESCO Bulgaria for the construction of the photovoltaic power plant (10 MW) on a territory of historical remediated landfill
- Detailed engineering for solar park number two and three finished
Status:
-
Done. The solar power plant was commissioned in March 2023
-
Construction started in Q1 2024
Environmental Protection milestones at Pirdop site
As part of our long-term Metals for Progress: Driving Sustainable Growth company strategy we began construction of two additional photovoltaic parks in April 2024. An additional expansion has already been approved. We have already been expanding the captive solar park since 2021, another investment in decarbonizing of our production. The measures will be implemented until 2024/25.
We are considerably increasing captive power generation with four photovoltaic plants that will cover around 15% of the site's electricity needs with green energy. Around 55,000 MWh of electricity will be generated every year, roughly the amount required to power a city of 25,000 people. And we will be avoiding around 25.000 t of CO2.
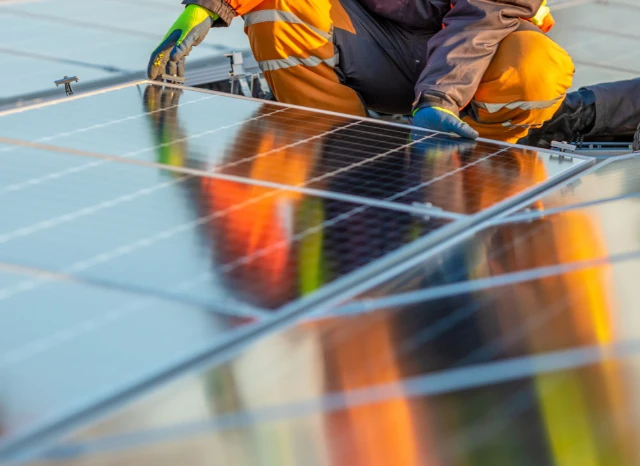
Solar farm: In July 2020, the contract was signed with CEZ ESCO Bulgaria EOOD, a company of the CEZ Group. The Aurubis-1 photovoltaic system at the Pirdop site optimizes the smelter’s external energy consumption by 11,000 MWh annually. The electricity generated is equivalent to the annual requirements of 3,500 households or a city with a population of 14,000. Compared with the use of coal-generated power, this will reduce CO2 emissions by 15,000 t per year – and over 225,000 t for the planned period of operation.
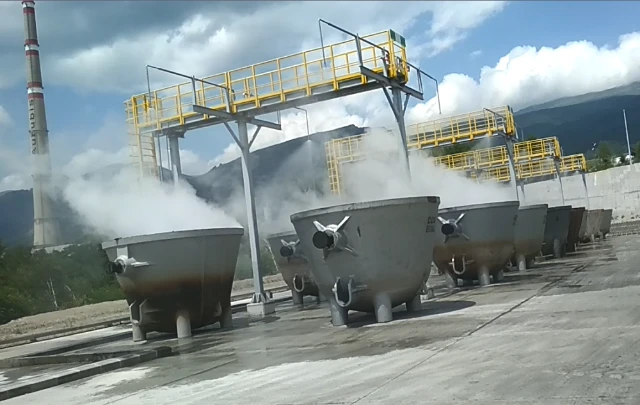
Converter slag cooling optimization: A new facility for cooling converter slag in pots was commissioned in early 2020. This project will be extended in the coming years in order to also optimize the flash smelter furnace slag cooling process.
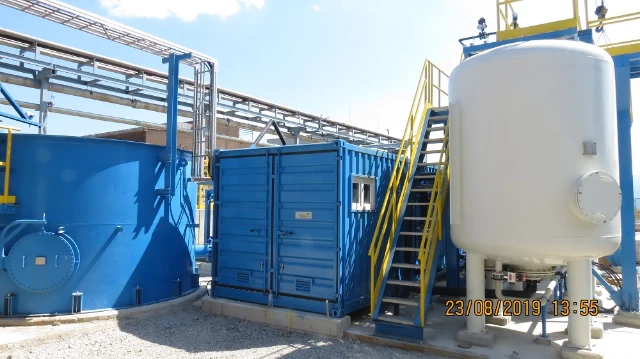
Industrial wastewater treatment plant modification: A new sand bed filter unit was installed in order to reduce the discharge of undissolved substances into bodies of water.

Expansion of fayalite landfill: The first stage of the fayalite landfill expansion was completed and commissioned in May 2018.
The objective of the project is to build an extension to the existing fayalite landfill that will consist of two cells with a total capacity of approximately 19.8 million tons. The cells are surrounded by soil that is protected by an insulating layer and equipped with a drainage system. Each cell will be built in eight separate stages up to the height of the existing fayalite landfill.
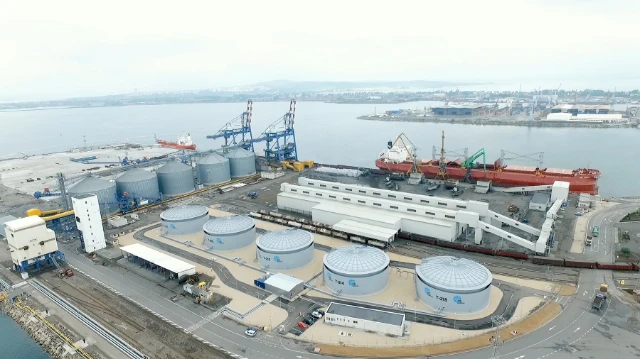
Special terminal for handling and storing sulfuric acid at the Port of Burgas: A new terminal for handling and storing sulfuric acid was officially inaugurated at the Port of Burgas on the Black Sea. The entire storage capacity is 50,000 tons of sulfuric acid.
Both projects (the terminal for sulfuric acid and the warehouse for copper raw materials) were implemented in cooperation with the largest private port operator in Bulgaria – BMF Port Burgas.
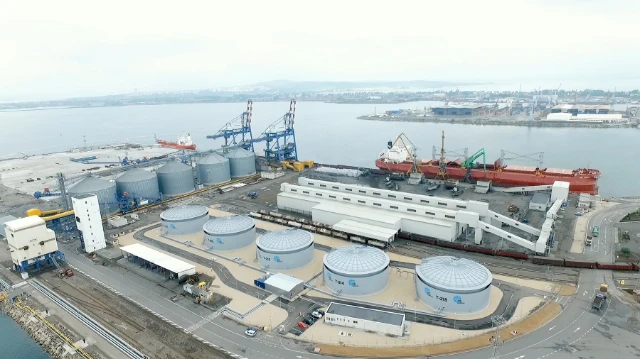
Warehouse for copper raw materials in the Port of Burgas: A new warehouse for copper raw materials opened at BMF Port Burgas in May 2017. The warehouse has a storage capacity of 65,000 tons of copper concentrates and covers an area of 6,000 m2. The focus of this project is on improving environmental performance when it comes to protecting the air. The new facilities enable the transport and storage of copper concentrates in closed rooms. In the process, bulk material is handled without losses. The current equipment uses the best available techniques (BAT).
Seveso permit issued: In August 2017, Aurubis Bulgaria successfully received the Seveso permit pursuant to Directive 2012/18/EU (Seveso-III).
Closure of the third sludge landfill: Similar to the first and second sludge landfills, the third sludge landfill for sludge from wastewater and off-gas treatment was successfully closed according to plan and in conformity with all applicable environmental requirements (especially Directive 1999/31/EC). The closed landfill will now be monitored for at least the next 30 years to ensure that all restoration work was successful.
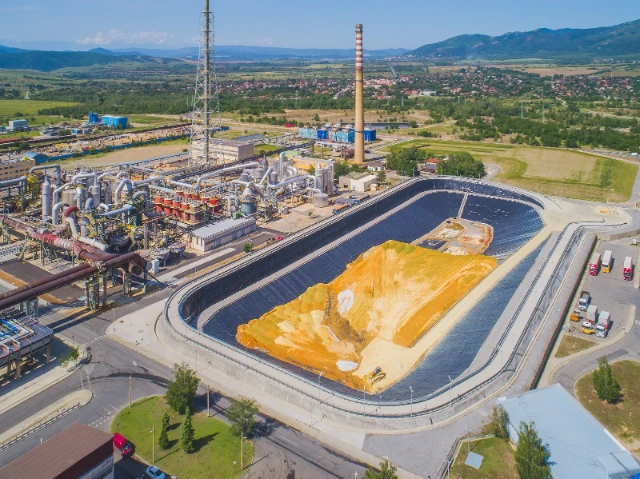
Construction of the fourth sludge landfill: The fourth special landfill for sludge from wastewater and off-gas treatment was constructed and commissioned in full conformity with all relevant environmental requirements (in particular Directive 1999/31/EC).
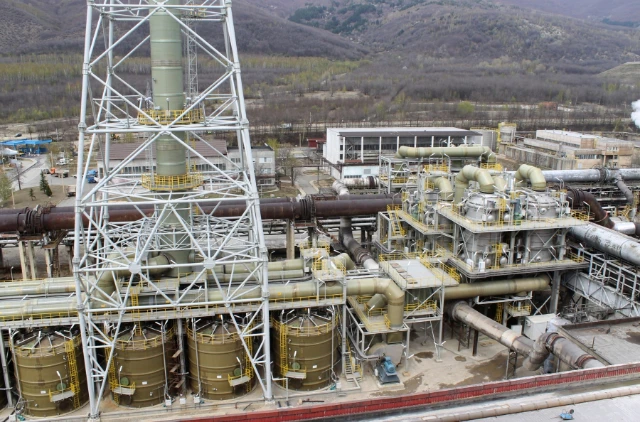
New additional treatment plant for secondary hood off-gases (Sulfacid): The new gas cleaning system (Sulfacid) was constructed and commissioned in full conformity with the best available techniques (BAT). The project makes a notable contribution to environmental protection. It uses a modern process, a technology called Sulfacid, that is unique for Bulgaria and for the entire copper smelting industry.
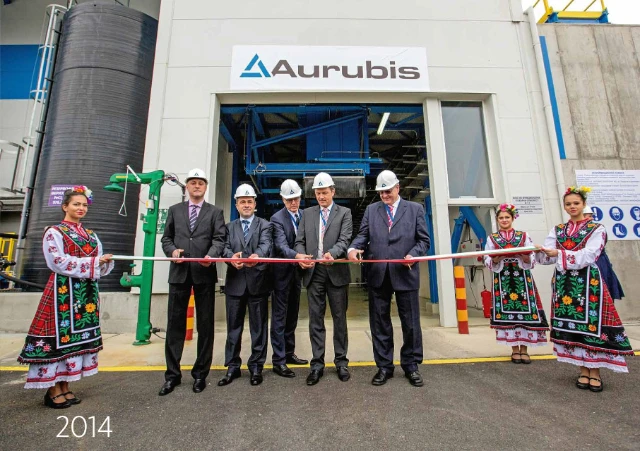
Opening of a rainwater treatment plant: Aurubis invested a total of € 6.3 million in the treatment plant for rainwater and drainage water. The building phase extended over a year and comprised the construction of the facility with a capacity of 250 m³/h and containment basins for accumulated wastewater. To decrease emissions to water sustainably, this plant cleans the rain and drainage water from the premises, which cover a surface of 4 km². The plant conforms to the best available techniques (BAT).
Use of waste materials and introduction of a new product in the portfolio: At the end of 2012, EU subsidies to Aurubis Bulgaria were approved for a project to recycle waste materials and to introduce a new product (fayalite/fine-grained iron silicate) to the portfolio. The project was financed by the EU Regional Development Fund as part of the program “Development of the Competitiveness of the Bulgarian Economy” (2007-2013) together with the Bulgarian government. The 50 % financial support is contractually guaranteed and is related to the regional development program category “Investments in Green Industries.” Among other things, the project includes the purchasing and commissioning of new equipment for copper scrap processing and a filter press for drying fayalite, which opens up additional possibilities for using this by-product.
Investment program “Aurubis Bulgaria 2014”: The project, which had a capital expenditure volume of € 44.2 million, included environmental protection measures amounting to € 26 million. The objective of the program was to improve the environmental balance of the smelting operations, in addition to process improvements. These improvements included the expansion of the filter capacity for the concentrate drying facility, the replacement of the concentrate burner, the expansion of the smelting furnace’s cooling equipment, and the modification and increase of the waste heat boiler’s heat exchange capacity. The construction of the new additional treatment plant for secondary hood off-gases was a considerable contribution the project made to environmental protection.
Reopening of the renovated Flotation Plant for slag: In addition to increasing the slag processing capacity, the copper recovery rate increased, which further improved the site’s resource efficiency. The best available techniques are used in the facility.
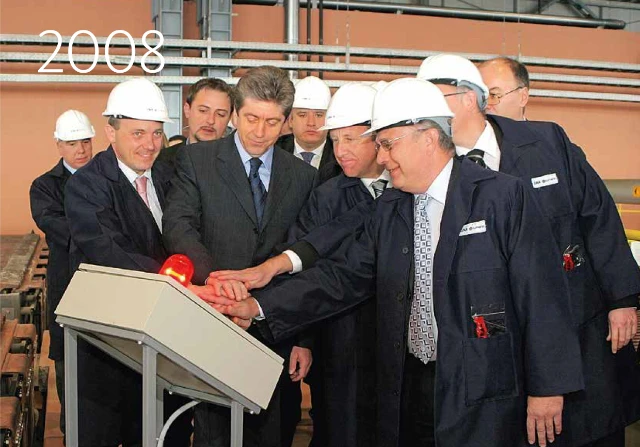
Opening of new Tankhouse: The new Tankhouse operates with fully automatic equipment and uses state-of-the-art technology pursuant to the ISA 2000 standard (Australia). The process is monitored and controlled by an automatic management system (DCS 7). The total costs for building the Tankhouse amounted to € 82 million, making it the largest industrial investment in Bulgaria at that time.
Construction of the third sludge landfill: The third landfill for sludge from wastewater and off-gas treatment was built and commissioned. The highest safety standards to protect the soil, surface water, and groundwater were fulfilled here as well (especially Directive 1999/31/EC).
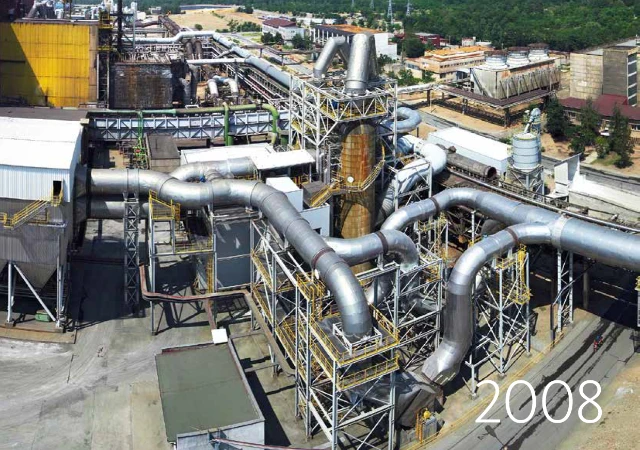
First conventional treatment system for secondary hood off-gases: In 2008, the first conventional treatment system for secondary hood off-gases was officially commissioned in full conformity with the best available techniques (BAT). The system notably reduces emissions of fine dust and sulfur dioxide. The total investment for the project amounted to € 14 million and was financed by Aurubis.

Certification of the environmental management system in accordance with ISO 14001: In March 2006, the environmental management system at the Pirdop site was successfully certified by an external auditor in accordance with the ISO 14001 standard for the first time.
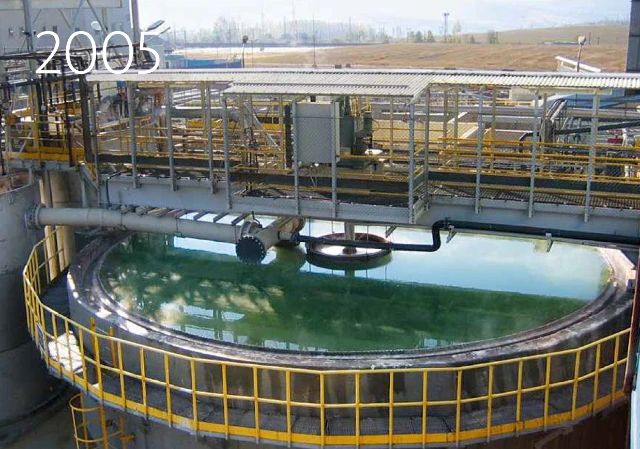
Opening of the second and third stages of the treatment plant for industrial wastewater: In 2005, the second and third stages of the treatment plant for industrial wastewater were commissioned. They use a modern technology that was developed to treat industrial wastewater in a three-stage process and that guarantees adherence to the limits for water emissions.
Upgrade of Sulfuric Acid Plant: The sulfur dioxide-rich gases that form during copper concentrate smelting in the flash smelter and at the converters are cleaned, dried, and converted into sulfuric acid in the Sulfuric Acid Plant. The facility consists of two identical units that produce concentrated sulfuric acid fully automatically. This is both used internally and sold for external use.
Implementation of the Directive concerning integrated pollution prevention and control (IPPC Directive): In June 2005, the plant’s environmental protection measures were recognized with a permit pursuant to the European IPPC Directive concerning integrated pollution prevention and control.
Construction of the second sludge landfill: The second landfill built especially for sludge from wastewater and off-gas treatment also fulfills all environmental requirements and the highest safety standards to protect the soil and groundwater (especially pursuant to Directive 1999/31/EC).
Belgian environmental protection prize: The successful completion of the environmental remediation program in Pirdop was distinguished with the 2003/2004 Belgian environmental protection prize in the category “International Cooperation for Sustainable Development.”

Construction of a fayalite landfill: A landfill was built to store fayalite, which accumulates in the flotation process. The landfill fulfills all environmental protection requirements. The first and second expansions of the landfill were completed in 2009 and 2015, respectively.
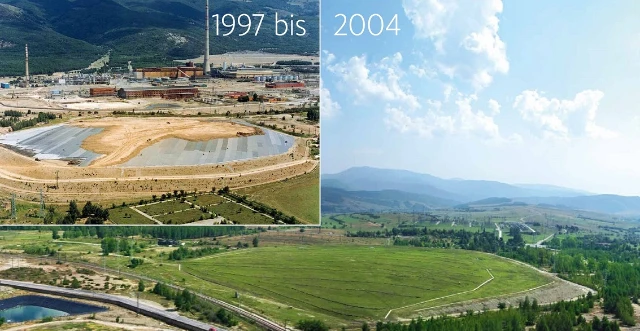
Environmental remediation program: The “Georgi Damyanov” smelter was operated as a state-owned company from 1958 to 1997. Due to inadequate investments in environmental protection by the Bulgarian government, there were considerable environmental impacts in the region during this time. The company was privatized in 1997 and managed by the Belgian Union Minière Group from that point. The privatization agreement included a remediation program amounting to US$ 25 million, among other things. Within the scope of this program, defunct facilities were torn down, building rubble was appropriately disposed of, and landfill areas (the sludge settling pond known as the “Blue Lagoon,” the fayalite landfill, the slag landfill) and contaminated soil were rehabilitated. In the course of the remediation program, the first stage of the treatment plant for industrial wastewater and the first landfill for sludge from wastewater and off-gas treatment were built and commissioned in 1999.
Certificates Aurubis Bulgaria
-
Um die heruntergeladene Komponente zu sehen den QR code scannen
ISO 9001: 2015
PDF
1 MB
-
Um die heruntergeladene Komponente zu sehen den QR code scannen
ISO 14001: 2015
PDF
1 MB
-
Um die heruntergeladene Komponente zu sehen den QR code scannen
ISO 45001 : 2018
PDF
1 MB
-
Um die heruntergeladene Komponente zu sehen den QR code scannen
ISO 50001 : 2018
PDF
2 MB
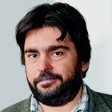
Ange Kostov
Environmental Department Manager
Phone | +359 728 62-203 |
Mobile | +359 885 350 284 |
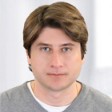
Krasimir Slavov
Enviromental Department Operational Manager
Phone | +359 728 62-514 |
Mobile | +359 887 707 524 |