
Environmental protection at the Pori site
The Aurubis Finland production site is located in the western part of Finland in the town of Pori next to the Kokemäenjoki River. The copper foundry and rolling mill are in a copper industrial park along with other companies that work with copper. The site comprises an area of about 78,000 m².
The rolling mill in Pori is a state-of-the-art hot and cold rolling mill, and it is fully integrated from casting to finishing. In 2023, our 310 employees produced 44,300 t of strip, sheet, plate and circles as well as 59,700 t of shapes, more than half of which for internal use. The selection of high-quality products covers a wide range of copper and copper alloys. Copper scrap is the main input for production, and recycling materials account for around 65 % of the raw materials used in the foundry. The waste heat that arises in the foundry is sold to local power plant Pori Energia. The waste heat produced during the hot rolling process is reused to preheat combustion air during processing. Emissions of dust and volatile organic compounds (VOCs) are reduced to a minimum using afterburning and filters in the foundry. Cooling water in the smelting process circulates in a closed system. Cooling and process water from the rolling mill is treated by an external service company, including the removal of copper and oil residues. In 2023, more than € 300,000 was invested in measures to improve our environmental performance.
Environmental Protection - facts & figures
At the beginning of January 2013, a project to improve the degree of filter house utilization started and improved the degree of utilization by about 5 % during 2013. Metal emissions in exhaust gases have fallen considerably over the years.
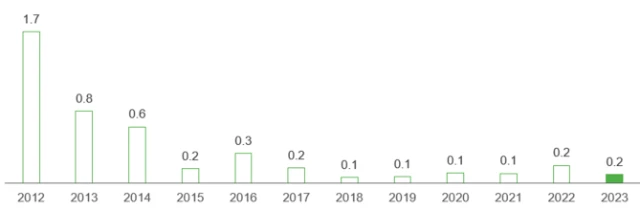
Metal emissions to air (Cu/Zn/Pb) in g/t of copper products
Total specific energy consumption in MWh/t of copper products sold is decreasing.
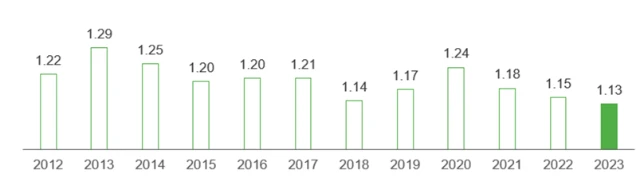
Total specific energy consumption MWh/t Cu of copper products
Environmental measures that have been implemented (“Milestones”)
-
Automatic online environmental reporting to monitor flue gas cleaning, afterburning and heat recovery.
- Copper: Replacement investment in picking line with new closed system to avoid Cu emissions to wastewater. First and second phase implemented, third phase planned for 2025
- Copper: Refurbishment of degreasing and pickling line in planning, some water management improvements implemented in 2023
- Copper: Renewal of wastewater measurement to avoid Cu emissions to the river.
Current important environmental targets and measures
Automatic online environmental reporting
Target:
- Filter house in use more than 98%
Date:
- 2022
Status:
-
Implemented on target
Replacement investment in pickling line
Target: Cu emission below 0,5 mg/l
Date:
- In progress
Implementation stage:
- Phase 1 and 2 implemented; Phase 3 planned
More pH measurements in rolling mill
Target: Cu emission below 0,5 mg/l
Date:
- 2023
Implementation stage:
- Implemented on target
New color-coded waste bins for paper and energy waste in rolling mill
Date:
- 2023
Status:
- Implemented on target
Extend emulsion usage time at cold rolling
Date:
- 2024
Status:
- Implemented
1. Heating system repairs and adjustment repairs at the rolling mill. Investigation into heat recovery
Date:
- 2025
Status:
- in progress
2. Changing energy monitoring system, improving the visibility of consumption data, and planning machine-specific savings
Date:
- 2025
Status:
- in progress
3. Reducing diesel consumption: replacing cars and diesel forklifts with electric cars and e-forklifts
Date:
- 2024
Status:
- Implemented
4. Replacing pre-heating furnace with electric one to reduce CO2 emissions
Date:
- 2030
Status:
- planning started
5. Integrating double-sided solar panels into the energy system
Date:
- 2024
Status:
- Implemented
Downloads (PDF)
-
Um die heruntergeladene Komponente zu sehen den QR code scannen
ISO 45001:2018
PDF
1 MB
-
Um die heruntergeladene Komponente zu sehen den QR code scannen
ISO 9001:2015
PDF
1 MB
-
Um die heruntergeladene Komponente zu sehen den QR code scannen
ISO 14001:2015
PDF
1 MB
-
Um die heruntergeladene Komponente zu sehen den QR code scannen
ISO 50001:2018
PDF
1 MB