
ContiRod® and SouthWire®
production processes
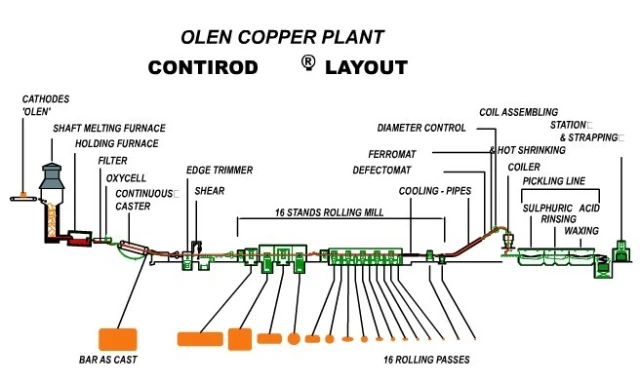
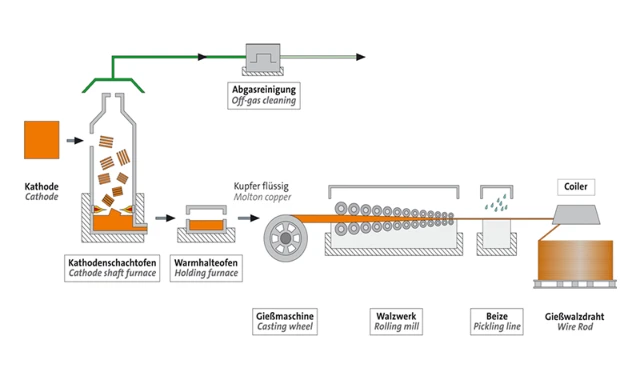
In both production methods, rod is produced in an integrated process that includes smelting, casting, rolling, cleaning and packaging. Aurubis constantly controls, monitors and develops these efficient and energy-optimized processes within narrow limits. The production process conforms to European and international standards and the product quality fulfills customers' stringent requirements.
After refining, copper is ready for further processing in its purest form, as a cathode. These cathodes with a copper content of more than 99.99 % are first melted down in a cathode shaft furnace under strict process monitoring. The 1,200 °C molten copper is then transferred via channels to the casting machine, the heart of the casting plant, where the copper is cast into an endless bar. There are two main casting machine technologies: Hazelett casting machines for ContiRod (see Graphic 1) and casting wheels for South Wire® casting machines (see Graphic 2), both of which are utilized in the Aurubis Group. Although the casting processes are different, the product is the same: a roughly 900 °C endless copper bar.
Still glowing red, the bar enters the rolling train, which consists of many roll stands. Rod diameters between 23.5 mm and 8 mm can be attained by constantly reducing the cross-section of the rolled material. The 400 to 500 °C wire is then surface-treated and cooled at a constant speed. The temperature is subsequently reduced to 40 °C. After it is dried and treated with a protective wax coating, the rod is wound into coils with a weight of 3.5 to 8 t. The continuous cast wire rod is now ready to be shipped to locations all over the world. Aurubis produces up to 800 of these coils per day.