
Umweltschutz am Standort Olen
Das Werk in Olen hat sich auf die Herstellung von Kathoden, Gießwalzdraht, sauerstofffreiem Gießwalzdraht sowie Stangen und Profilen spezialisiert.
In den letzten Jahren hat der Standort erfolgreich den Einsatz von Recyclingmaterialien erhöht. Diese Steigerung bringt allerdings höhere Anforderungen an die Behandlung von Luftemissionen mit sich, sodass hier umfangreiche Maßnahmen ergriffen werden.
Die Verbesserung des Umweltschutzes ist und bleibt ein sehr wichtiges Ziel in Olen. Seit 2000 wurden mehr als 70 Mio. € in den Umweltschutz investiert.
Eines der wichtigsten Projekte der letzten Jahre ist die neue Anlage zur Be- und Entladung von Binnenschiffen mit Containern (Cu-Port), die 2020 gebaut wurde. Transporte, die zuvor per LKW durchgeführt wurden, werden nun auf dem Wasserweg abgewickelt. Dadurch werden insgesamt etwa 20.000 Lkw-Bewegungen pro Jahr und damit über 230 t CO2-Emissionen pro Jahr vermieden. Darüber hinaus führt das Projekt zu einer Verminderung der Lärmemissionen am Standort und in der Umgebung.
Im Jahr 2016 wurden am Standort vier 200 Meter hohe Windräder gebaut und in Betrieb genommen. Das Investitionsprojekt mit einem Gesamtvolumen von 20 Mio. € ist eine Kooperation mit einem Partner aus dem Energiesektor und zwei Industrieunternehmen einschließlich Aurubis. Jede Einheit hat eine Kapazität von 3,5 Megawatt (insgesamt 14 Megawatt). Diese Windkraftanlagen liefern jährlich 30 Mio. kWh Strom, der direkt an den Standorten der Industrieprojektpartner genutzt wird und die CO2-Emissionen reduziert. Darüber hinaus werden Forschungs- und Entwicklungsprojekte zur Bestimmung und Umsetzung von Maßnahmen durchgeführt, um die europäischen Green-Deal-Anforderungen zu erfüllen und eine nachhaltige Energieversorgung des Standorts Olen für die Zukunft sicherzustellen. Zusätzlich zur Windenergieerzeugung vor Ort wurde 2023 ein Stromabnahmevertrag für 105.120 MWh abgeschlossen, um die CO₂-Emissionen weiter zu reduzieren. Im Jahr 2024 wurden 375 kWh Solarpaneele auf den Dächern installiert, und für 2025 ist eine weitere Solaranlage mit 1.200 kWh geplant, die den Standort Olen jährlich mit 1.260 MWh grüner Energie versorgt.
Ein weiterer Schwerpunkt des Standorts ist die Reduzierung von Metallemissionen und der Auswirkungen unserer Produktion auf Gewässer. Um die Belastung des Naturschutzgebiets Olens Broek durch gereinigte Abwässer aus der Abwasserbehandlungsanlage des Standorts zu vermeiden, wurde 2015 eine neue Abwasserleitung in Betrieb genommen. Mit dieser Leitung wurde der ehemalige Abwasserkanal, der durch das Naturschutzgebiet verlief, außer Betrieb genommen, und das Naturschutzgebiet wird durch die neue Abwasserleitung komplett umgangen. Zudem wurde die Einleitungsstelle so gewählt, dass ein Einfluss auf das Naturschutzgebiet aufgrund der Fließrichtung des Flusses ausgeschlossen ist.
Die Einführung eines Umweltmanagementsystems nach ISO 14001 begann 1998 in der Drahtanlage. Seit 2006 ist das Umweltmanagementsystem für alle Aktivitäten von Aurubis Belgien nach ISO 14001 zertifiziert. Im Jahr 2020 wurde das Energiemanagementsystem, das bis dahin Teil des Umweltmanagementsystems war, erweitert, aufgewertet und nach ISO 50001 zertifiziert. Das Qualitätsmanagementsystem gemäß ISO 9001 sowie das Gesundheits- und Sicherheitsmanagementsystem nach ISO 45001 ist ebenfalls seit Mitte 2021 zertifiziert.
Umweltschutz Olen - Daten & Fakten
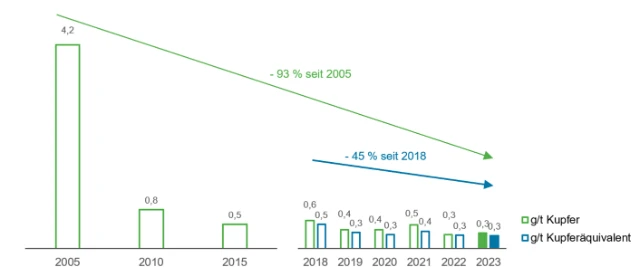
Metallemissionen in Gewässer in g/t erzeugten Kupfers und in g/t Kupferäquivalent
Die Metallemissionen in Gewässer pro erzeugter Tonne Kupfer konnten seit 2004 um 93 % reduziert werden.
Die Metallemissionen in Gewässer wurden über die Jahre erheblich reduziert. Das Hauptaugenmerk liegt nun auf der kontinuierlichen Verbesserung der Leistungsfähigkeit der Abwasserbehandlungsanlage und der Verbesserung der Vorbehandlung der Abwasserströme am Entstehungsort in der Produktion, um die Eingangsfracht zur Abwasserbehandlungsanlage zu senken. Darüber hinaus wird am Standort ein Wassermanagementprojekt umgesetzt, um die Entnahme von Frischwasser zu reduzieren, die Wassereinleitungsmengen zu verringern und die Wiederverwendung von Regenwasser zu maximieren.
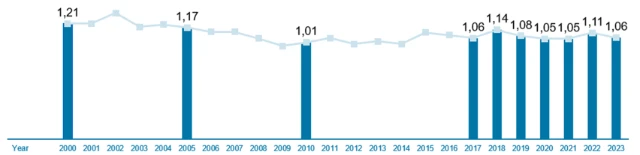
Energieverbrauch [MWh/t] pro erzeugter Tonne Kupfer
Energieverbrauch [MWh/t] pro erzeugter Tonne Kupfer konnte seit 2000 um 8 % reduziert werden
Heute können nur vergleichsweise kleine Verbesserungen innerhalb der Werksgrenzen erzielt werden, da der Reduzierung des Energieverbrauchs und der Emissionen technologische Grenzen gesetzt sind. Im Rahmen einer Vereinbarung mit den flämischen Behörden wurden kosteneffizienten Maßnahmen zur Energiereduzierung bereits umgesetzt. Hierzu gehört die Ausrüstung der Drahtanlage mit zusätzlichen Ventilatoren mit energieeffizienten Frequenzreglern und die Installation einer Frequenzsteuerung für die Emulsionspumpe.
In der Drahtanlage in Olen wird Nachspülwasser bereits mit Kondensat aus dem Dampf der Lufterhitzer erwärmt, um den Energieverbrauch weiter zu senken. Am Hauptofen wurde zudem ein neuer Wärmetauscher zur Erwärmung des Kesselspeisewassers mit den Abgasen des Rückgewinnungskessels installiert.
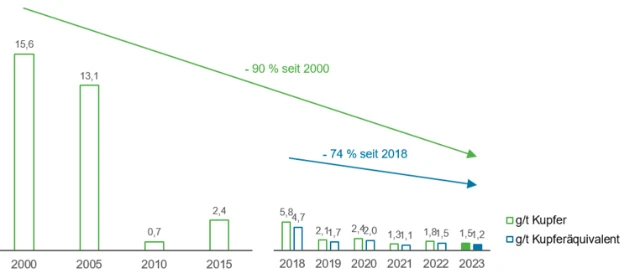
Staubemissionen in g/t erzeugten Kupfers und in g/t Kupferäquivalent
Die Staubemissionen pro erzeugter Tonne Kupfer konnten seit 2000 um 90 % reduziert werden.
Weitere Reduzierungen der Staubemissionen wurden mit der Umsetzung eines neuen Filterkonzepts erreicht. Im Jahr 2020 haben wir ein neues Quenchsystem in Kombination mit einem Schlauchfilter installiert und an den Hauptofen angeschlossen
Maßnahmen & Projekte im Umweltschutz
Nächste Schritte:
-
Weitere Verringerung der in das Abwasser abgegebenen Schadstoffe auf Abteilungs-/Anlagenniveau (vor der Endbehandlung in der Abwasserbehandlungsanlage).
Status:
-
Arbeiten laufen
Grad der Implementierung:
-
Erfolgreiche Zertifizierung am 15. Juli 2020. Erfolgreiche Rezertifizierung am 15. Juli 2023.
Status:
-
Umgesetzt
Nächste Schritte:
-
Austausch von Dach und Fassaden von zwei Gebäuden im GJ 2020/21 und 2021/22.
Status:
-
Umgesetzt
Nächste Schritte:
-
Austausch des Abgasfilters und der Quenche im Jahr 2020 durchgeführt. Die derzeitigen Ergebnisse sind vielversprechend.
Status:
-
Umgesetzt
Nächste Schritte:
-
Die Elektrogewinnungsanlage im Bereich der Drahtanlage wurde ausgetauscht. Verringerung der Säurekonzentration in der Beizanlage durchgeführt.
Status:
-
Umgesetzt
Nächste Schritte:
-
Spezielle Sicherheitsschränke für brennbare Flüssigkeiten und Aerosole in der gesamten Anlage installiert.
Status:
-
Umgesetzt
Nächste Schritte:
- Pyrolyseofen in Betrieb zur Vorbehandlung und Entfernung von organischem Material aus reinem Kupferschrott, damit dieser direkt in den Contirod-Ofen gegeben werden kann
Status:
- Umgesetzt
Nächste Schritte:
-
Mit Fertigstellung des BOB-Projektes kann der Standort Olen sowohl Bleed aus der eigenen Elektrolyse als auch Bleed vom Standort in Beerse vor Ort in Olen verarbeiten und spart somit LKW-Transporte und Prozesszeit. Der gereinigte Elektrolyt, der der Elektrolyse zugeführt wird, schließt somit den Kreislauf am Standort Olen (siehe Abschnitt "Meilenstein" für weitere Einzelheiten).
Status:
-
In Betrieb genommen
Implementierungsgrad/Datum/Nächste Schritte:
- Um zusätzliche sekundäre Abgase aufzufangen und zu behandeln, wurde an der Hütte ein neuer Schlauchfilter installiert. Derzeit läuft eine Studie zur Entwicklung zusätzlicher Absaugsysteme, um weitere diffuse Emissionen zu erfassen und so die Auswirkungen der Standortaktivitäten auf die Umwelt weiter zu verringern.
Status:
- Teilweise in Betrieb genommen
Meilensteine im Umweltschutz am Standort Olen
Im Juni 2024 wurde eine neue Solaranlage mit einer Kapazität von 375 kWp in Betrieb genommen, die jährlich etwa 300 MWh an erneuerbarer Energie liefert. Diese Initiative unterstützt die laufenden Bemühungen von Aurubis Olen, die Energieeffizienz zu verbessern und die CO₂-Emissionen zu reduzieren, und stärkt das Engagement des Standorts für Nachhaltigkeit weiter.
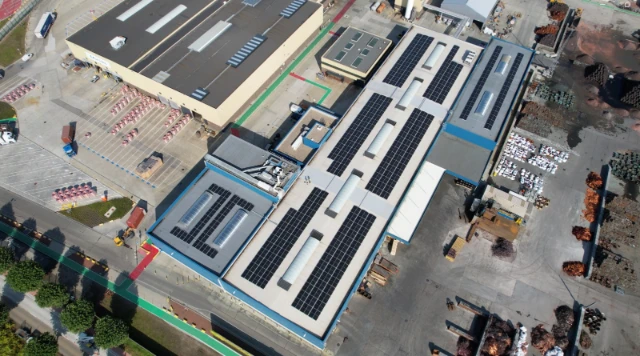

Im Mai 2024 wurden zusätzliche sekundäre Absaughauben in der Anodenproduktionsanlage in Betrieb genommen. Zunächst wurden diese zusätzlichen Abgase durch eine temporäre Filteranlage gefiltert. Seit November 2024 ist die endgültige neue Filteranlage in Betrieb. Damit ist Aurubis Olen in der Lage, noch mehr sekundäre Abgase abzufangen und die Umweltauswirkungen der Anlage weiter zu reduzieren.
Eine weitere Verbesserung in diesem Zusammenhang ist die Installation eines Wassersprühsystems auf dem Schlackenbrecher- und Verladebereich.

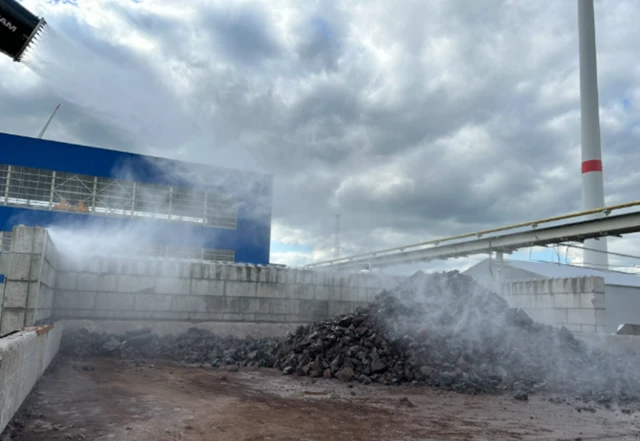
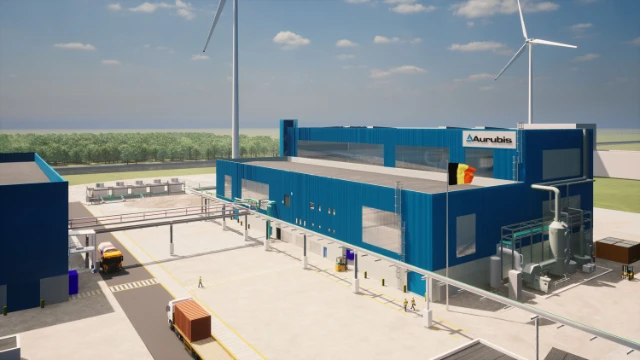
Am 24. November 2022 erhielt Aurubis Olen die Genehmigung für den Bau und die Nutzung einer Anlage zur Behandlung von Bleed vor Ort am Standort - Bleed Olen Beerse (BOB). Ab Mitte 2024 wird der Standort in Olen mithilfe des BOB-Projektes, Bleed aus der Elektrolyse in Olen und den Bleed aus der Elektrolyse des Standortes in Beerse vor Ort in Olen zu verarbeiten. Derzeit wird Bleed aus Olen per LKW nach Deutschland transportiert und die aufbereitete Säure ebenfalls über den Straßenverkehr wieder zurück nach Olen transportiert.
Neben der erheblichen Reduzierung der Transportwege über Straßen, wird das BOB-Projekt die Verfahrensdauer verkürzen, der gereinigte Elektrolyt für die Elektrolyse in Olen bereitstellen, somit den Kreislauf der Anlage in Olen schließen und erheblich zum Umwelt- und Ressourcenschutz des Standortes beitragen.
Anfang 2023 wurde eine neue Schrottpresse in Betrieb genommen. Die neue Presse erzeugt weniger Lärm und Vibrationen und befindet sich näher und mehr in der Ecke der Lärmschutzwand. Da der größte Teil des eingehenden Kupferschrotts von der neuen Ballenpresse verarbeitet wird, kommt es zu einer spürbar geringeren Belastung für die Nachbarschaft.
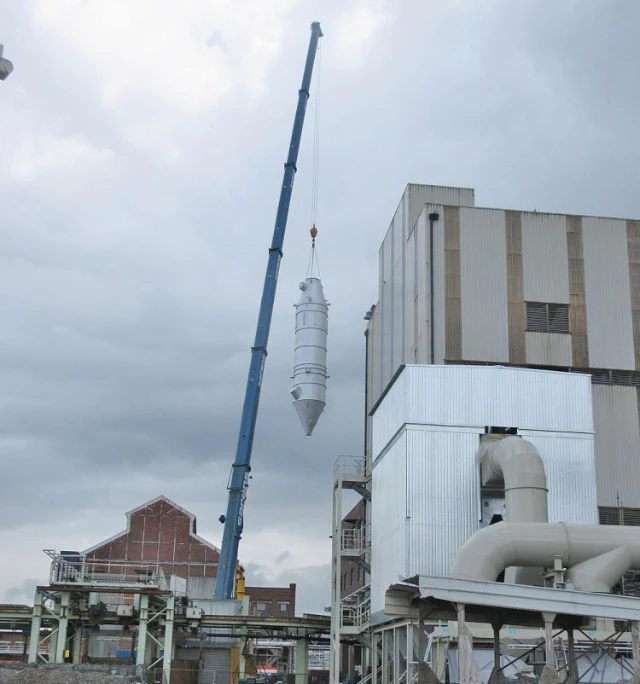
Im Sommer 2020 wurde die erste Phase des Projektes zur Verbesserung der Abgasreinigung am Hauptofen (Contimelt) realisiert. Ein komplett neuer Abgasfilter und eine neue Quenche, die direkt am Ausgang des Anodenschachtofens positioniert ist, verbessern die Abgasreinigung und reduziert Emissionen. Zur weiteren Verbesserung wird im Jahr 2021 ein neues gekapseltes Beladungssystem zur Beschickung des Ofens installiert.
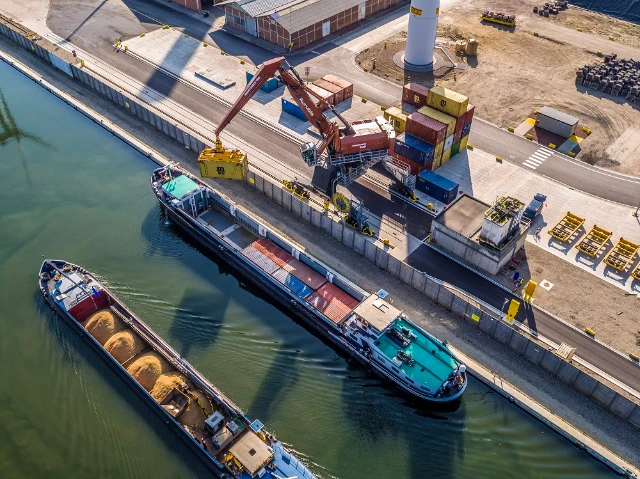
Bis Anfang 2020 wurden alle Container, hauptsächlich mit Altkupfer, per LKW in das Werk transportiert. Nur ein Teil der ankommenden Blister und Anoden wurde bereits per Bahn und Wasserstraße angeliefert. Im März 2020 wurden ein neuer Kai und Kran in Betrieb genommen. Am Standort in Olen können nun bis zu 10.000 Container pro Jahr über Binnenschiffe angeliefert und verschifft werden. Damit werden die Zufahrtsstraßen zum Werk um 20.000 LKW-Bewegungen pro Jahr entlastet und so eine wichtige Verkehrsverlagerung realisiert.
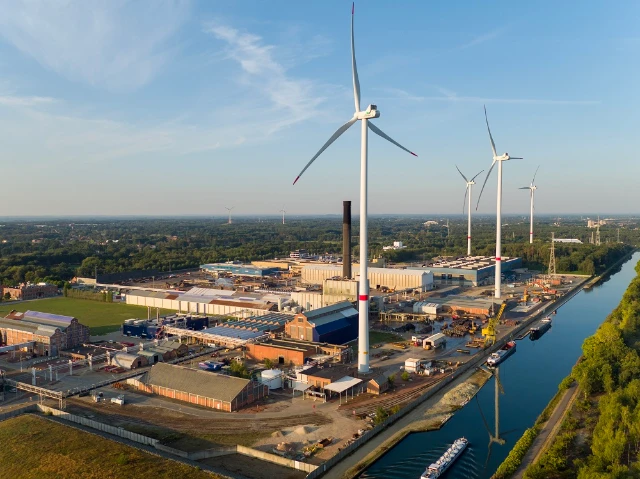
In Zusammenarbeit mit einem benachbarten Unternehmen und dem Energieversorger unseres Werkes wurden 2016 vier riesige Windräder auf und in der Nähe des Werkes errichtet. Diese Windturbinen mit einer Rotorspitzenhöhe von 200 Metern liefern 14 MW grünen Strom für das Werk in Olen und reduzieren den CO2-Fußabdruck um 24.500 Tonnen, was dem Stromverbrauch von mehr als 9.000 Haushalten entspricht.
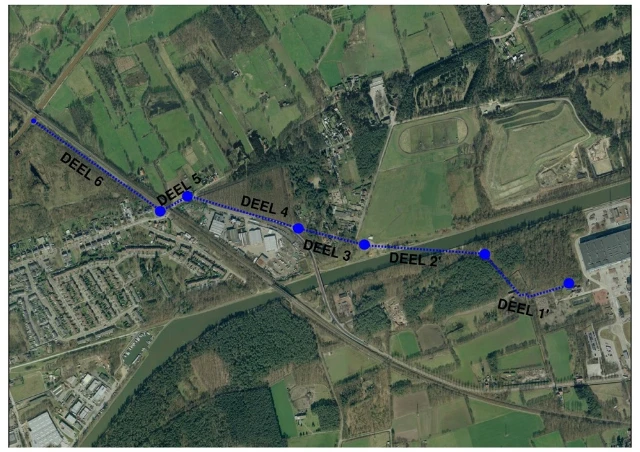
Ende 2015 wurde eine knapp 2 km lange Abwasserpipeline in Betrieb genommen. Diese Rohrleitung transportiert das gereinigte Abwasser der Abwasserbehandlungsanlage direkt in den Fluss Kleine Nete und entlastet damit ein Naturschutzgebiet nördlich des Aurubis-Werks.
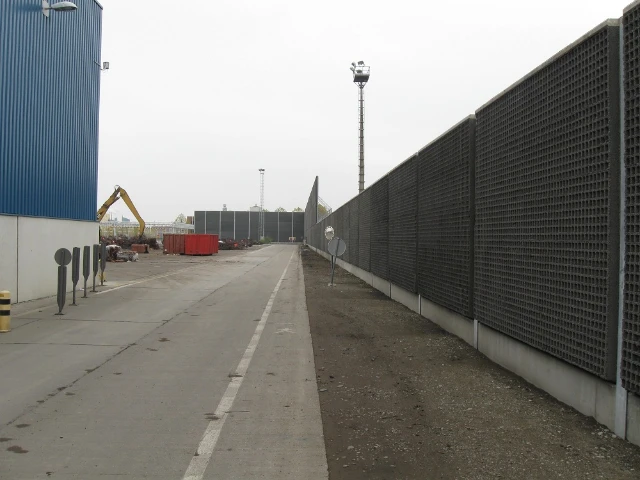
Um die Lärmbelastung durch die Schrottentladung und die Ballenpresse zu reduzieren, wurde 2012 eine Lärmschutzwand entlang der Hauptstraße in der Nähe des Werks errichtet, die zu einer Lärmminderung für die benachbarten Häuser von 20 dB(A) führt. Der Schalldruckpegel wird mit jeder Reduzierung um 3 dB halbiert.
Zertifikate Aurubis Olen
-
Um die heruntergeladene Komponente zu sehen den QR code scannen
ISO 9001:2015
PDF
1 MB
-
Um die heruntergeladene Komponente zu sehen den QR code scannen
ISO 14001:2015
PDF
1 MB
-
Um die heruntergeladene Komponente zu sehen den QR code scannen
ISO 50001:2018
PDF
1 MB