
Iron silicate fines (Fayalite)
Iron silicate fines, also called fayalite, is a by-product produced by Aurubis Bulgaria, with universal application in variety of areas in construction. Received by complicated metallurgical process it has stable physical and chemical characteristics.
Properties of iron silicate fines make it compatible with various materials like limestone, clay, clinker, cement, sand, gravel, chemicals, etc. Its’ application transfer building materials to those with lower environmental impact and reduced utilization of natural resources.
Material is certified as by-product by the Ministry of Environment and Water in October 2021. No additional environmental permits are required by the building material producers.
Iron silicate fines is applied for the main areas of construction in reinforce concrete buildings and facilities: starting from the structural elements, through brick walls till finishing works like plasters and coatings for buildings and facilities.
Iron-silicate fines is a universal source of raw materials applied in variety of applications, making final products with better performance.
Basic characteristics: |
|
Particle shape |
angular |
Appearance |
Anthracite |
Bulk density |
1800 kg/m^3 |
Specific density |
3700 kg/m^3 |
Moisture content |
Two types: 12 % & 1% |
Loss of ignition |
0,01% |
Friction angel |
At moisture 12 % – 70% lower than 1 % – 45% |
Composition: |
|
Element |
Typical range |
Fe elem. |
46% (as Fe2O3>60 %) |
SiO2 |
27% |
Al2O3 |
3.20% |
CaO |
1.80% |
MgO |
0.70% |
Zn |
1.50% |
Cu |
0.42% |
S |
0.36% |
Applications:
Cement clinker with iron silicate fines (ISF)
Portland cement clinker production consumes large amounts of natural resources, mostly limestone and clay, but also sand and iron additives. Nowadays, the cement industry is facing the challenge of protecting the environment by decreasing CO2 emissions which reflect to reduced consumption of natural raw materials.
Various industrial solid wastes have been utilized as alternative raw materials in Portland cement clinker production. Iron silicate fines (ISF) are such alternative material, which can be used as a substitute of the commonly used iron ores. According to the mineral composition of the main raw materials (clay and limestone), ISF could be used as iron and silica corrective material or as a source of iron.
There are several benefits of ISF valorisation in the cement industry:
- Ready-to-use source of iron;
- No need for additional crushing and grinding;
- Suitable for both dry and wet clinker production lines;
- Good mixing properties;
- Promote lower calcination temperature;
- Eliminate the need for mineralizers.
The chemical composition of the material includes the minerals fayalite, magnetite, pyroxene and quartz, basically in the form of ferrous and silica dioxide, which give the name of the material – iron silicate.
Element |
Typical value |
Range |
Fe |
46,0% (Fe2O3>60 %) |
(44,0÷48,0)% |
SiO2 |
27,0% |
(26,0÷28,0)% |
Al2O3 |
3.20% |
(2,7÷3,7)% |
CaO |
1.80% |
(1,3÷2,5)% |
MgO |
0.70% |
(0,6÷1,1)% |
Zn |
1.50% |
(0,9÷2,8)% |
Cu |
0.42% |
(0,36÷0,48)% |
S |
0.36% |
(0,25÷0,55)% |
ISF contractors are: Heidelberg Cement, Lafarge Holcim, Titan, American Cement, etc.
Ready-mix concrete with iron silicate fines
Ready-mixed concrete is the most widely used types of concrete, manufactured in a batch plant, according to each specific job requirements, then delivered to the job site ready to be used. Ready-mix concrete is often used instead of other materials due to the wide range of uses in buildings, particularly in large projects like building, bridges, facilities, etc. By utilization of iron silicate fines, ready-mix concrete improves his characteristics both in fresh and hardened state by making substantial durability in time. No cracks, no pores and smooth surface makes iron silicate fines perfect additive to every project.
There are many applications of ISF in ready mixed concrete:
- Structural elements of the buildings (beams, columns, slabs, foundations);
- Bridges (piers, slabs, beams)and tunnels;
- Marine structures (coast protection, retaining walls, etc.);
- Exposed concrete (walls, slabs, beams, staircases).
There are several benefits of ISF valorization in ready-mixed concrete:
- Increased strength and density of concrete;
- Improved durability, especially waterproofing (Cw0,8 & Cd50 (BNS EN 206:2013 & NA.N)) and protection against the aggressive impact of chlorides, sulphates and salts
- Concrete volume stability (no shrinkage, no swelling);
- Reduced heat of hydration;
- Increased abrasion resistance (18±0,2cm3/50cm2 (BNS EN 13892-3:2015));
- Significantly increased frost resistance (∆m=0,2% & ∆f=2,3% (BNS EN 206:2013+A1:2016)).
- Certified as a concrete aggregate according to EN 12620:2002+A1:2008;
ISF heavy concrete
Iron silicate fines is applied in heavy concrete for civil and industrial structures, where there is a need for high density and heavy weight facilities. Although its heavy weight, heavy concrete with iron silicate fines has good workability and great density.
There are many applications of ISF heavy concrete:
- Heavy foundations for structures and facilities;
- Underground and tunnelling;
- Marine structures (coast protection, retaining walls, tetrapods, etc.);
- Bridges;
- Anchorages;
- Coatings for pipelines;
- Lego Blocks.
There are several benefits of ISF valorization in heavy concrete:
- Increased strength and density of concrete (about 2,8kg/m3);
- Improved durability, especially waterproofing (Cw0,8 & Cd50 (BNS EN 206:2013 & NA.N)) and protection against the aggressive impact of chlorides, sulphates and salts
- Concrete volume stability (no shrinkage, no swelling);
- Reduced heat of hydration;
- Increased abrasion resistance (18±0,2cm3/50cm2 (BNS EN 13892-3:2015));
- Significantly increased frost resistance (∆m=0,2% & ∆f=2,3% (BNS EN 206:2013+A1:2016)).
- Certified as a concrete aggregate according to EN 12620:2002+A1:2008;
ISF shielding concrete
ISF shielding concrete is a building material used for the construction of protection shields. These shields guarantee the work safety of the people inside, subjected to different radiations and attacks.
This type of concrete is used for:
- walls, ceilings and floors against ionizing radiation;
- multi-threat protection from electromagnetic radiation;
- radiation protection in hospitals, laboratories, oncology clinics and waste treatment facilities;
- protection against the hazard of nuclear radiation leakage;
- protection against terrorist attacks;
- protection against extreme natural disasters.
There are several benefits of ISF valorization in shielding concrete:
- Combines structure and shielding system;
- Increases strength and density of concrete (about 2,8kg/m3);
- Decreases maintenance and increase durability of structures;
- Reduction of size while maintaining high protection capacity;
- Thermal insulation capacity;
- Sustainable and cost effective.
ISF ultra high performance concrete
Ultra High Performance Concrete (UHPC) is characterized by a very high compressive strength (above 150 MPa) and extreme durability, even when exposed to high aggressive environmental impacts. All these characteristics make it an alternative to other construction materials (e.g. steel) for the construction of transport and hydraulic facilities, high-rise buildings, as well as for special mine structures, structures for military application and high aesthetic architectural elements and details. At the same time, UHPC is a material, which complies with the policy of sustainable development by reducing the need for maintenance and rehabilitation of the facilities.
Iron silicate fines (ISF) are one of the best materials for making UHPC, which bring plenty of benefits in the structures and elements:
- Compact the macro- and microstructure due to its small grain size;
- Increase the density by additional interaction with other ingredients;
- Increase the workability of the fresh mixtures;
- Reduce natural raw material utilization;
- Create long-term life products;
- Make sustainable final products.
The density of ISF UHPC is about 2,4 kg/m3 and the compressive strength exceeds 100MPa. In case thermal treatment is applied, the mechanical properties of concrete could increase by 30%. For application in thin structural elements subjected to flexture, it is recommended to use short (6 to 8 mm) steel fibres – 2% by volume.
ISF deicing concrete
De-icing concrete is a special mixture containing ingredients, which are electrically conductive. Ordinary concrete does not have this property. The composition of de-icing concrete consists of high quantities of iron-silicate fines (ISF) in combination with other geological materials with high iron content and a cocktail of building materials.
When de-icing concrete is connected to a power source its ingredients are heated and prevent ice formation on concrete surface. This special type of concrete is used on several US bridges and sidewalks and is invented by Prof. Christopher Tuan and assigned by the University of Nebraska with Patent No.: US 6,825,444 B1. The concrete surface is heated up to +20°Celsius above the ambient temperature.
There are several benefits of ISF valorization in de-icing concrete:
- Source of electrically conductive components;
- Improves the mechanical and durability properties of concrete;
- Certified building material according to EN 12620:2002+A1:2008;
- Sustainable building material.
ISF paving concrete products
Vibro-pressed concrete products are widely distributed in urban areas. The technology of their production requires a concrete mix design with specific workability and flowability of the fresh concrete mix and at the same time high mechanical properties and durability of the hardened products. Alternative materials, which in general improve the properties of hardened concrete, could be effectively utilized in paving products, if they cover the requirements for low water-cement ratio and formability of elements.
Iron-silicate fines (ISF) improve the compaction rate of the products thanks to their small grain size, which leads to improved appearance and durability. ISF can be used for a wide range of concrete products like tiles, blocks, panels, curbs, etc.
There are several benefits of ISF valorization in paving products:
- Improved mechanical properties (up to 25%);
- Better durability due to compacted structure and possible pozzolanic activity of ISF with cement;
- Improved abrasion resistance (14±0,2cm3/50cm2 (BNS EN 1338:2005, app. H));
- Volume stability, no risk of alkali-silica reaction;
- Certified building material according to EN 12620:2002+A1:2008;
- Sustainable building material.
ISF anti-skid surface coatings
Anti-skid coatings (ASC) refer to a surface treatment of roads by providing improved top surface skid resistance. Normally the thickness of the coating is about 3-5 mm and helps drivers brake under emergency conditions at hazardous locations.
Ordinary ASC contains natural bauxite as an aggregate for surfaces subjected to high friction. Although there is an increasing interest in ASC, natural bauxite stops the development of such coatings, because of its very high price and rarity.
Iron silicate fines (ISF) can substitute natural bauxite in ASC and make geopolymer concrete with better properties. The Polished Stone Value (PSV) is a coefficient which defines road resistance to skidding. ISF improve the PSV value and the abrasion resistance of synthetic geopolymer in general. University of Ulster, Northern Ireland are responsible for current research and development of ISF ASC, according to EN and ASTM standards.
There are several benefits of ISF valorization in anti-skid surface coating:
- Improved abrasion resistance;
- Improved compressive strength;
- Reduce high price of anti-skid surface coatings;
- Sustainable building material.
ISF dry mixtures
Dry mortars or dry-mixed mortars are made of cement, sand, mineral and chemical additives, mixing together proportionally. They are often in powder or granule form pre-mixed in special factory and transported to construction site in paper sacks or by cement trucks. After stirring with certain amount of water, they can be used directly. Fine structure of iron-silicate fines is a benefit for dry mortars, because it improves workability of mortars and keeps the consistency in time.
There are usually two kinds of dry mortars - normal type and purposed type. Normal type includes masonry mortar, plastering mortar and ground mortar and special purposed ones: tile adhesive, interface dry powder, insulating mortar, self-leveling, water-proof mortar, repair mortar, wall putty, etc.
There are several benefits of ISF valorization in dry mortars:
- Improves fresh properties;
- Improves mechanical characteristics in hardened state;
- Absent of linear deformations;
- Reduced shrinkage;
- Certified material according to EN 13139:2002/AC:2004.
ISF ceramic products
Ceramic is one of the most ancient building materials on our planet, dating from earlier than 10 000 years BC. Once humans found that clay mixed with water could be moulded and then fired, they started experimenting with different shapes, colours and mix designs.
Nowadays, scientists and the industry have been testing a wide range of alternative materials for ceramic production, which improve the properties of the final products on the one hand and reduce the extraction of natural resources on the other.
Iron silicate fines (ISF) is such a material, which utilization leads to several benefits in different types of ceramic products (bricks, ceramic and clinker tiles & plates, roof tiles, etc.):
- Increase mechanical properties;
- Increase volume stability;
- Decrease plasticity during drying;
- Decrease linear shrinkage;
- Increasing sound and thermal insulation properties;
- Decreasing fossil fuels for the burning process, with results in decreasing CO2 release and burning costs.
Downloads
-
Um die heruntergeladene Komponente zu sehen den QR code scannen
Certificate of conformity of the factory production control EN
PDF
1 MB
-
Um die heruntergeladene Komponente zu sehen den QR code scannen
Declaration of performance EN 12620
PDF
2 MB
-
Um die heruntergeladene Komponente zu sehen den QR code scannen
Declaration of performance EN 13139
PDF
2 MB
-
Um die heruntergeladene Komponente zu sehen den QR code scannen
Iron Silicate Fines Construction Brochure EN
PDF
10 MB
-
Um die heruntergeladene Komponente zu sehen den QR code scannen
Iron Silicate Fines Specification EN
PDF
1 MB
Downloads
-
Um die heruntergeladene Komponente zu sehen den QR code scannen
Iron Silicate Fines Logistics EN
PDF
1 MB
-
Um die heruntergeladene Komponente zu sehen den QR code scannen
Iron Silicate Fines Process Card EN
PDF
1 MB
-
Um die heruntergeladene Komponente zu sehen den QR code scannen
Iron Silicate Fines Safety Information Sheet EN
PDF
1 MB
-
Um die heruntergeladene Komponente zu sehen den QR code scannen
Iron Silicate Fines Visuals EN
PDF
1 MB
-
Um die heruntergeladene Komponente zu sehen den QR code scannen
European Technical Assessment ISF 2023
PDF
5 MB
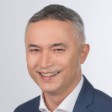
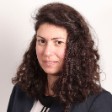